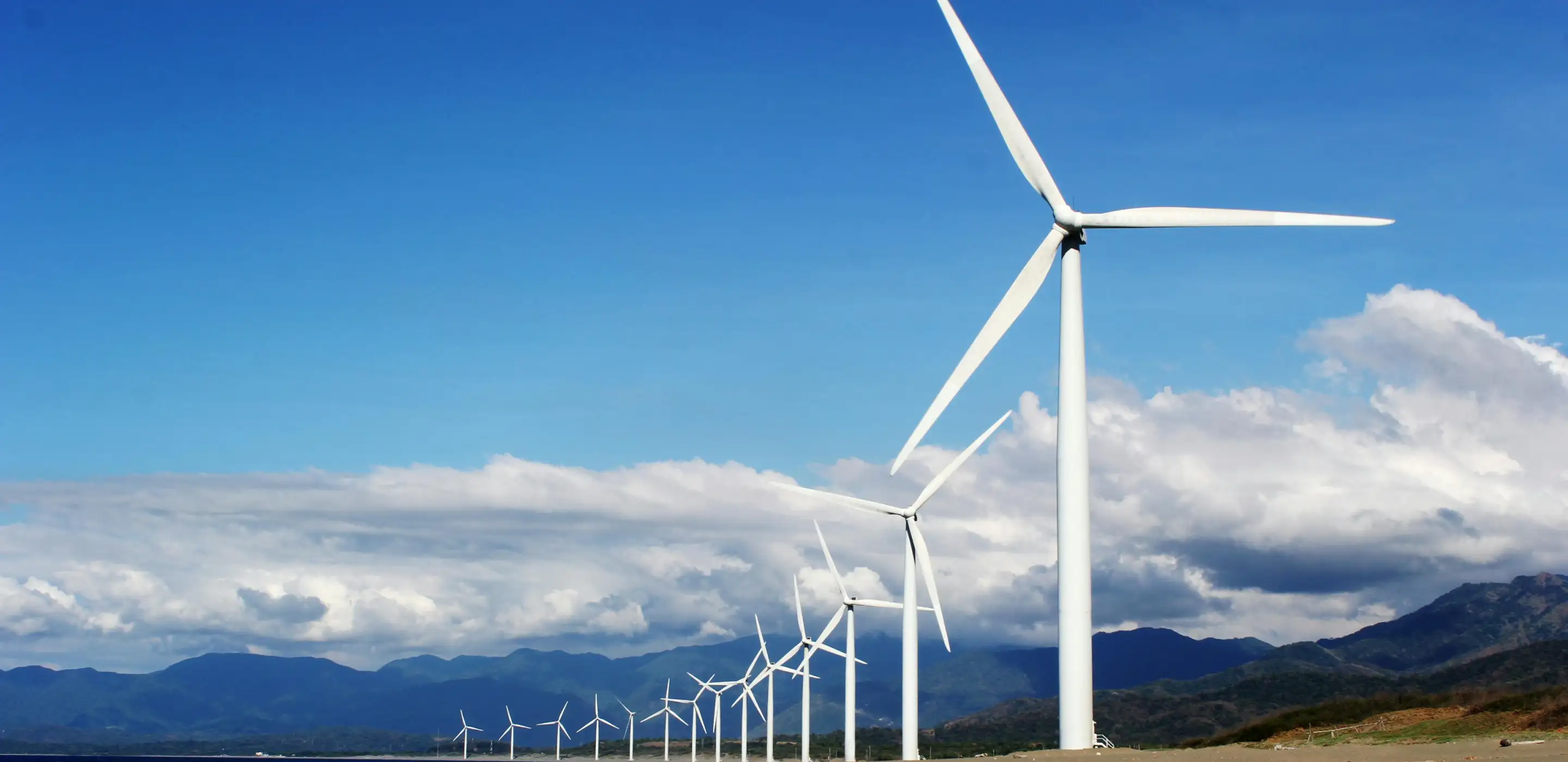
Hands on control and monitoring?
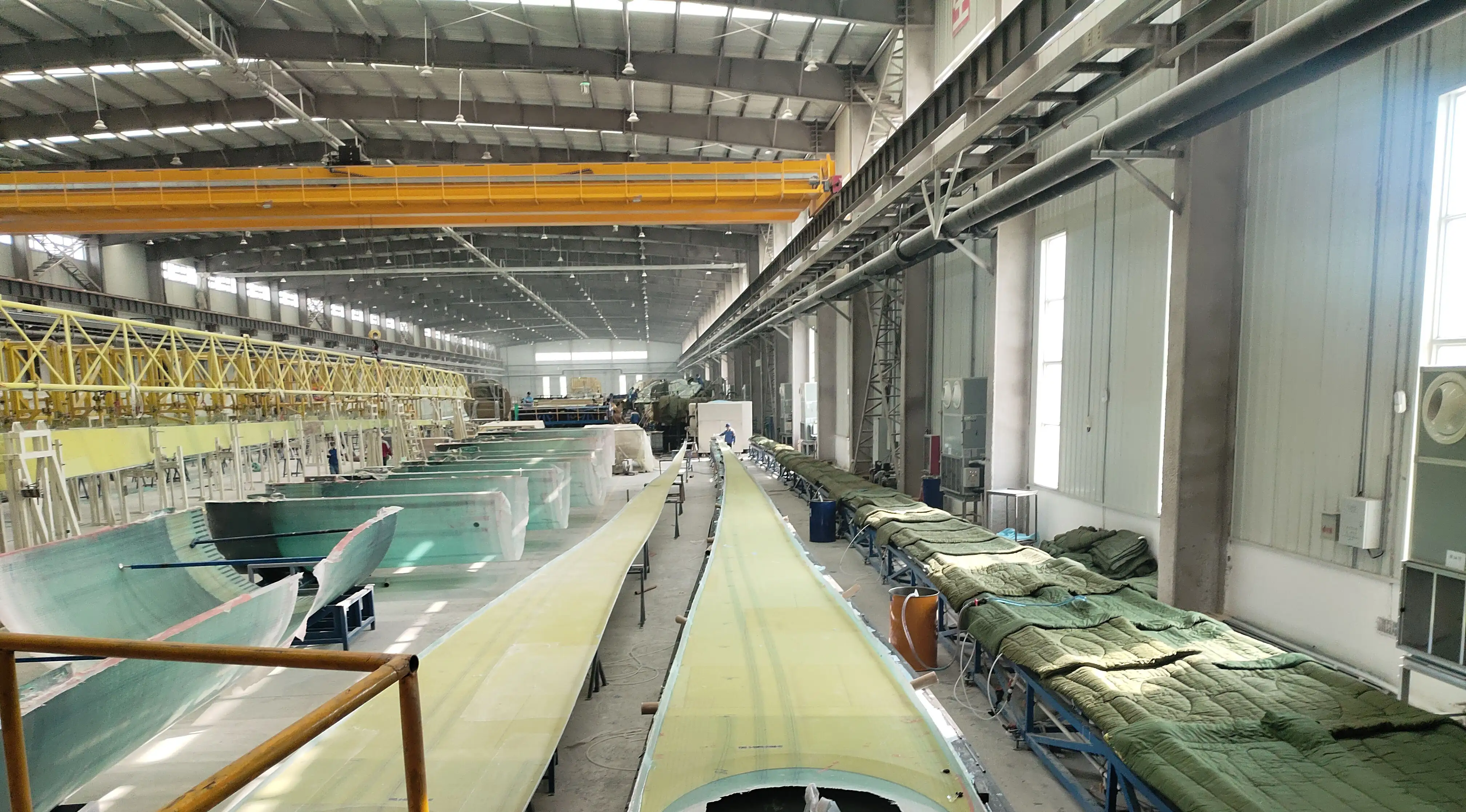
Composite materials are widely utilized in the wind energy sector. Gas permeability testing of these materials is primarily conducted to assess their ability to prevent the penetration of gases or liquids, ensuring optimal product performance in various environmental conditions.
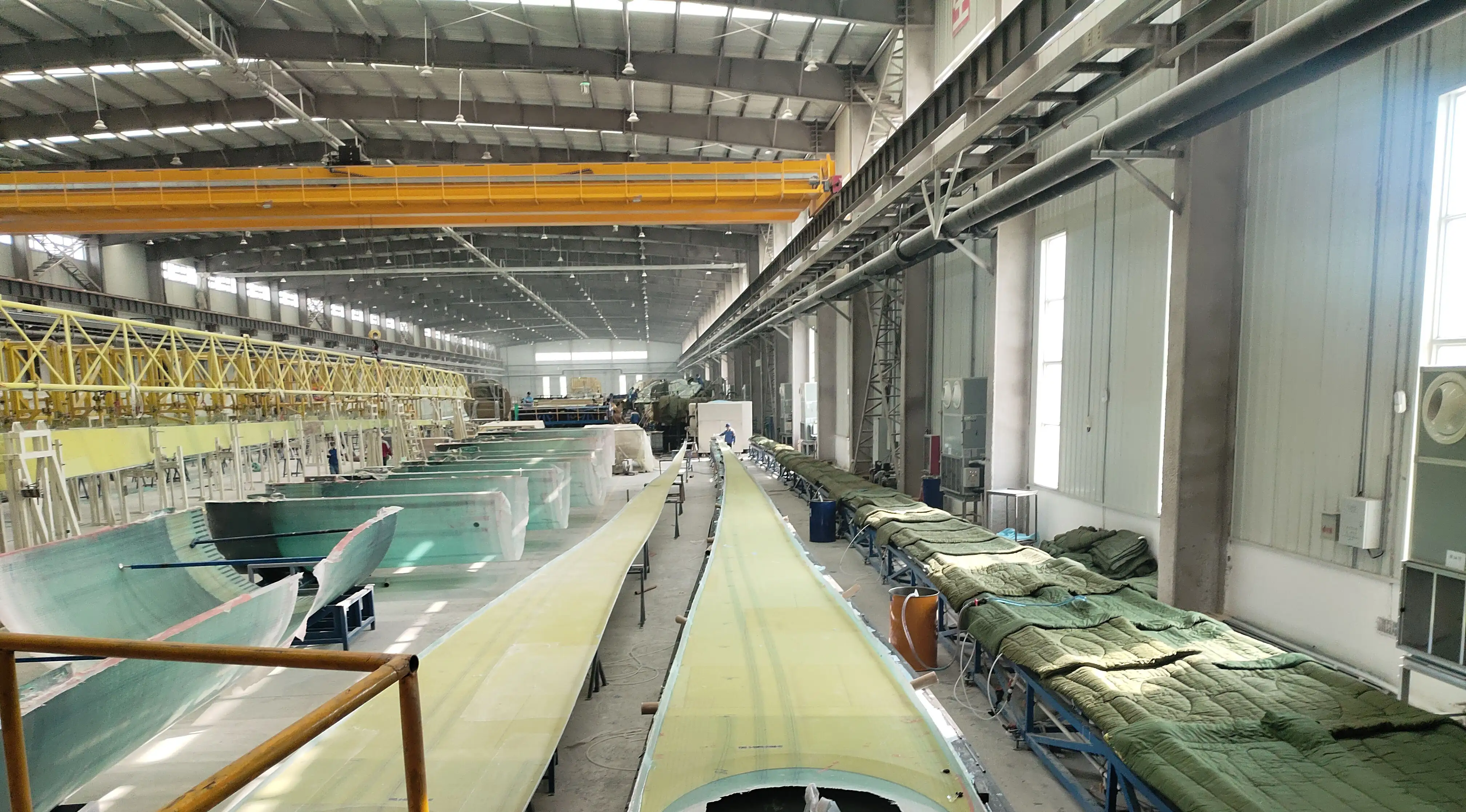
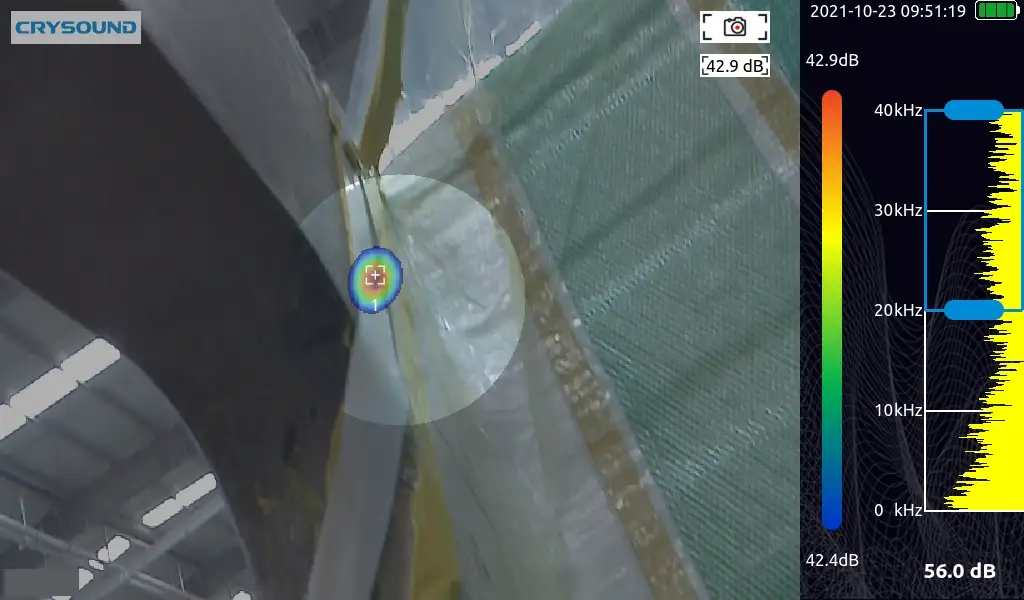
Vacuum leaks produce ultrasonic waves, which are captured by the microphone array of the CRYSOUND acoustic imaging device. By processing these signals in real time, the device can quickly and accurately pinpoint the exact location of leaks. This technology allows anyone to perform comprehensive, reliable, and actionable leak detection with ease.
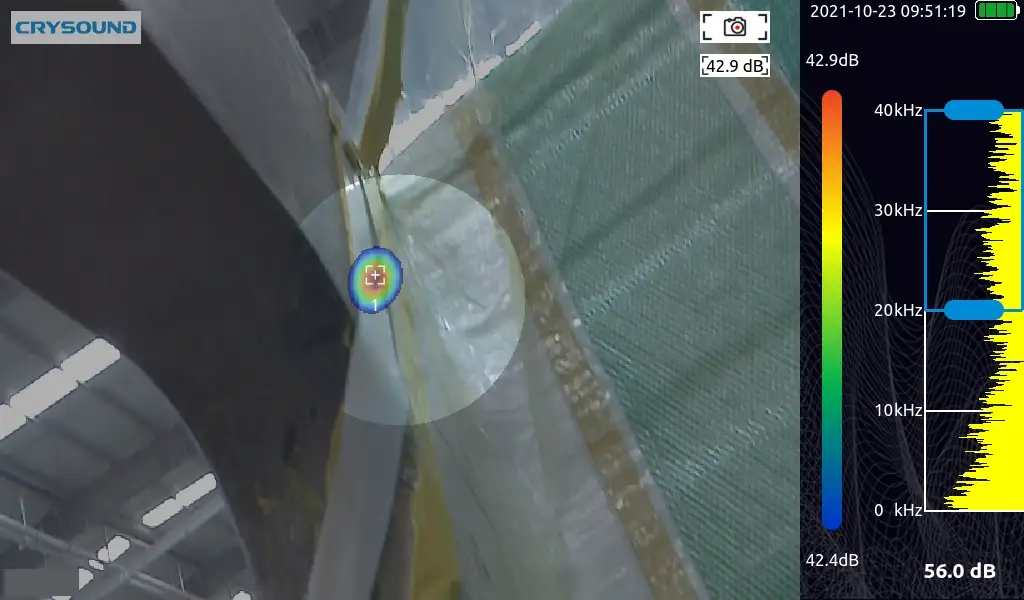
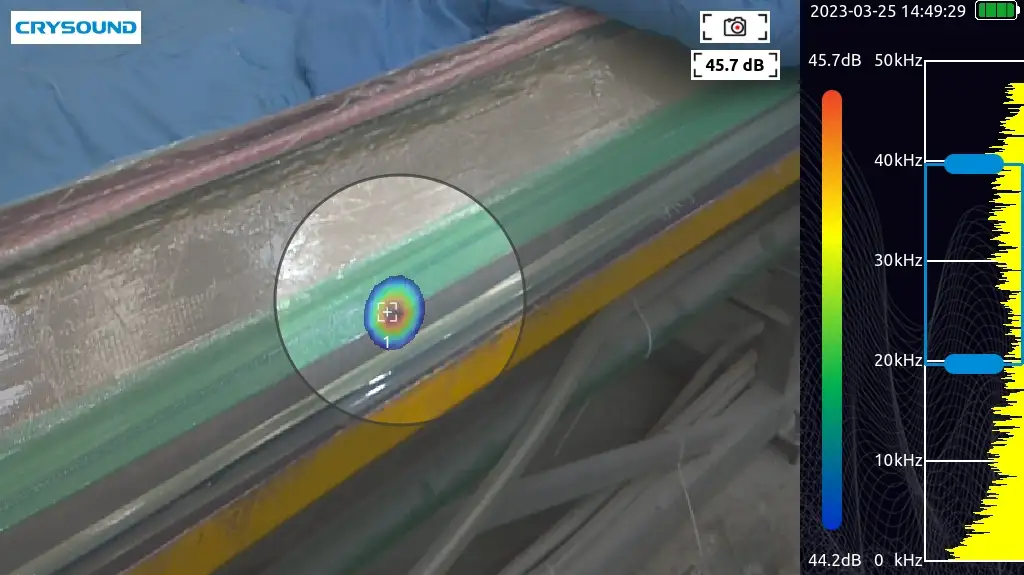
No-contact scanning and testing of mating sealing surfaces from a distance enable non-destructive air-tightness testing of vehicles and vessels.
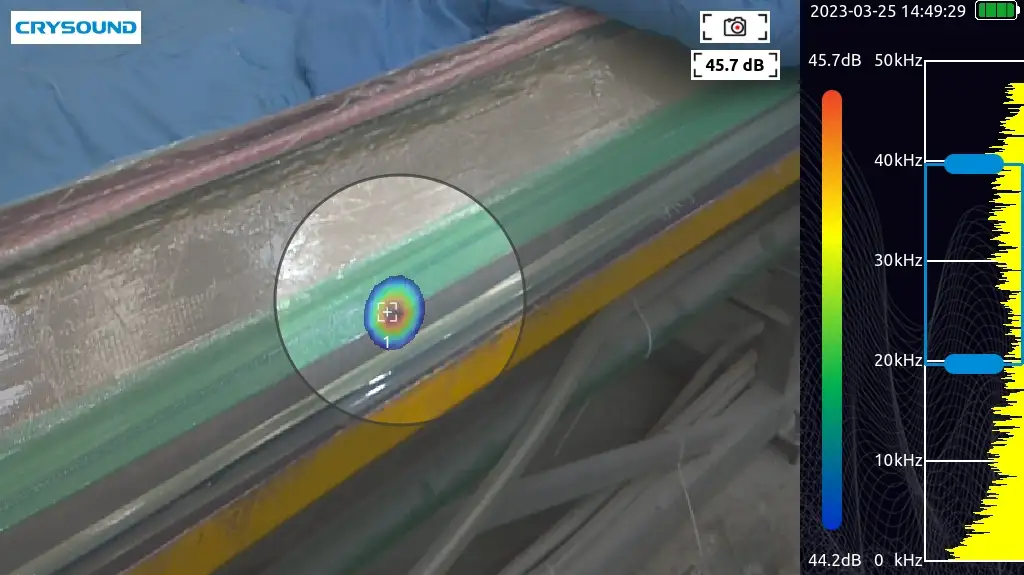

Acoustic imaging is a novel technology that provides a real-time visualization of leaks from a distance. With an acoustic imaging camera, anyone can pinpoint vacuum leaks 10x faster than traditional methods.

Composite materials are widely utilized in the wind energy sector. Gas permeability testing of these materials is primarily conducted to assess their ability to prevent the penetration of gases or liquids, ensuring optimal product performance in various environmental conditions.
Composite materials are widely utilized in the wind energy sector. Gas permeability testing of these materials is primarily conducted to assess their ability to prevent the penetration of gases or liquids, ensuring optimal product performance in various environmental conditions.
Composite materials are widely utilized in the wind energy sector. Gas permeability testing of these materials is primarily conducted to assess their ability to prevent the penetration of gases or liquids, ensuring optimal product performance in various environmental conditions.
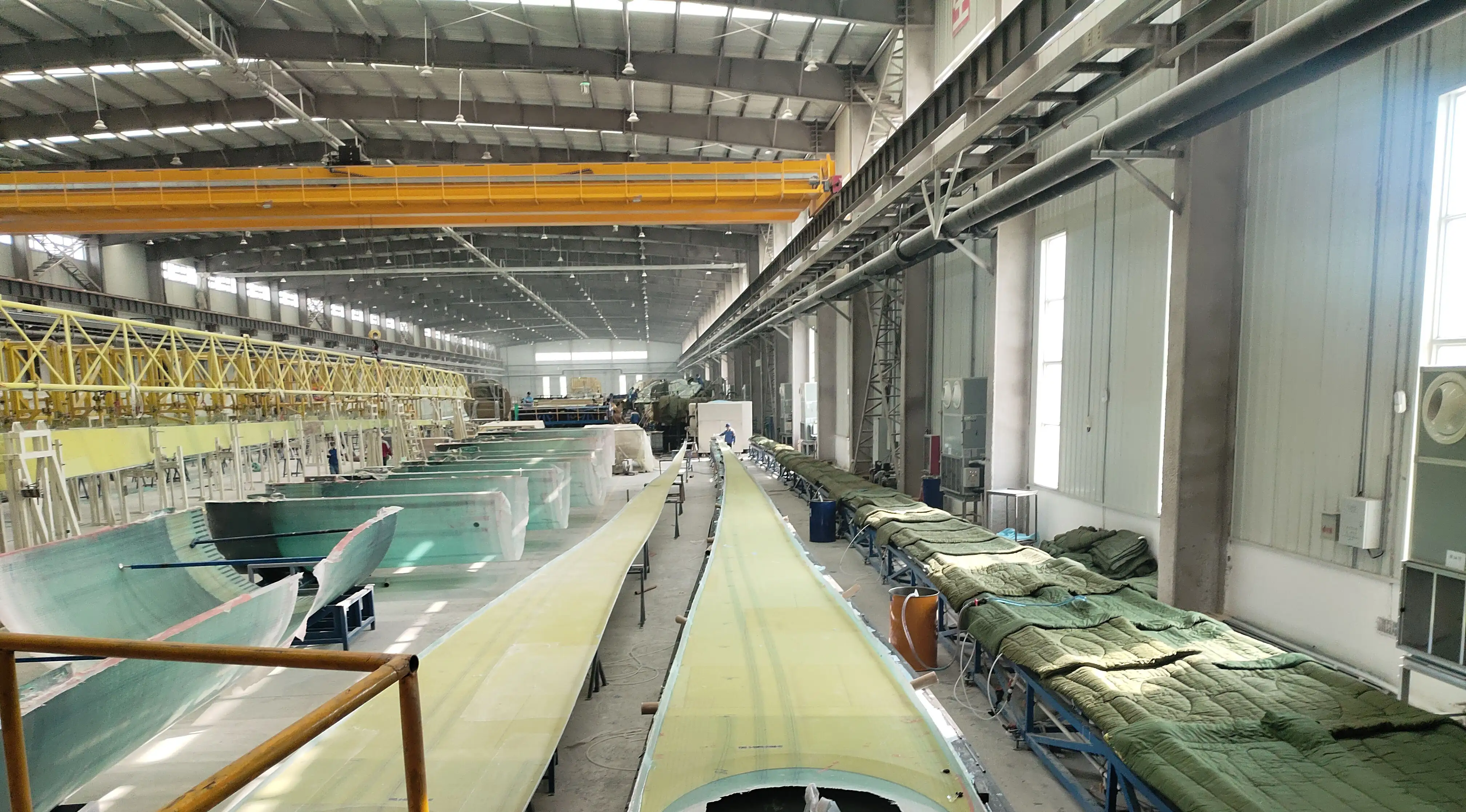
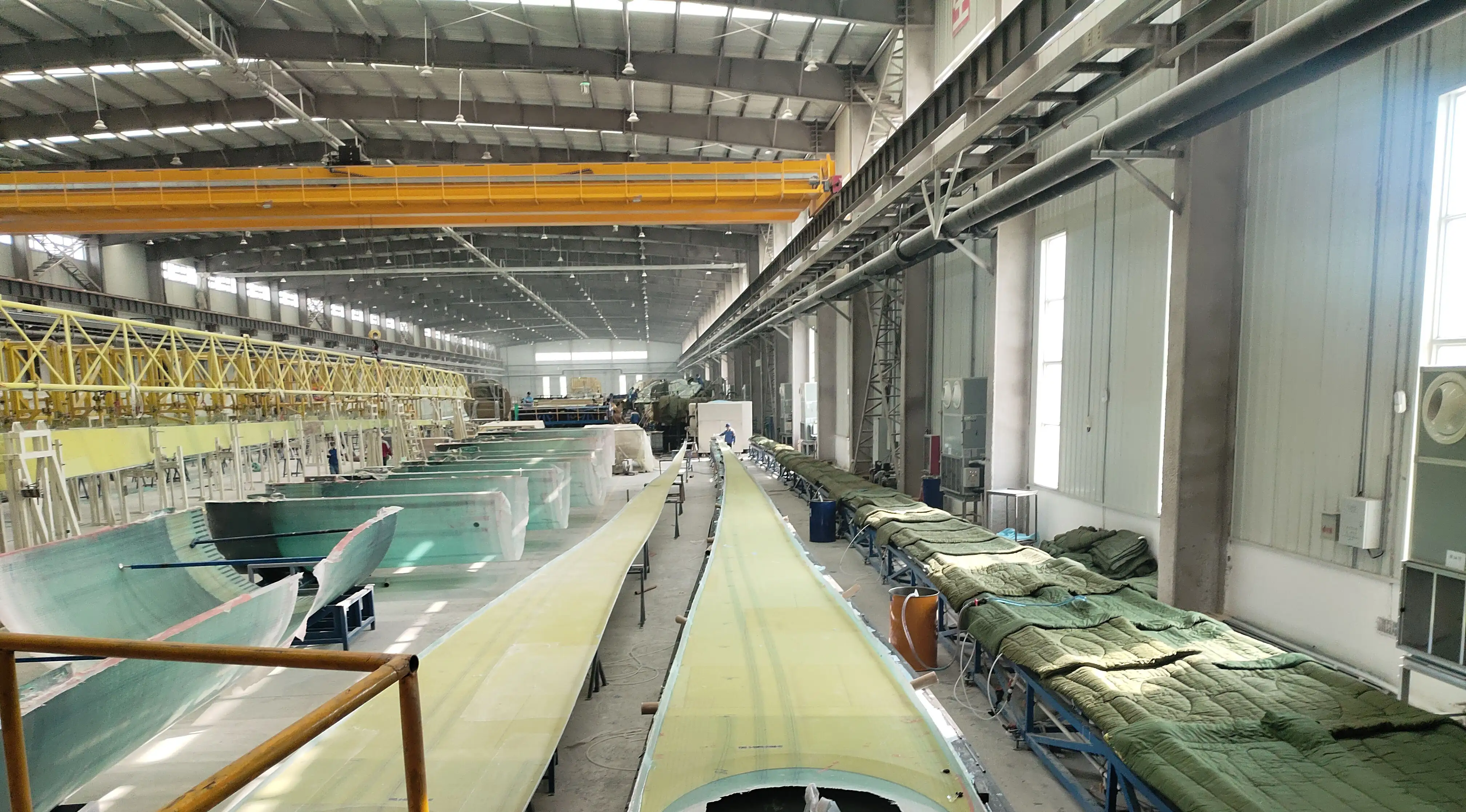
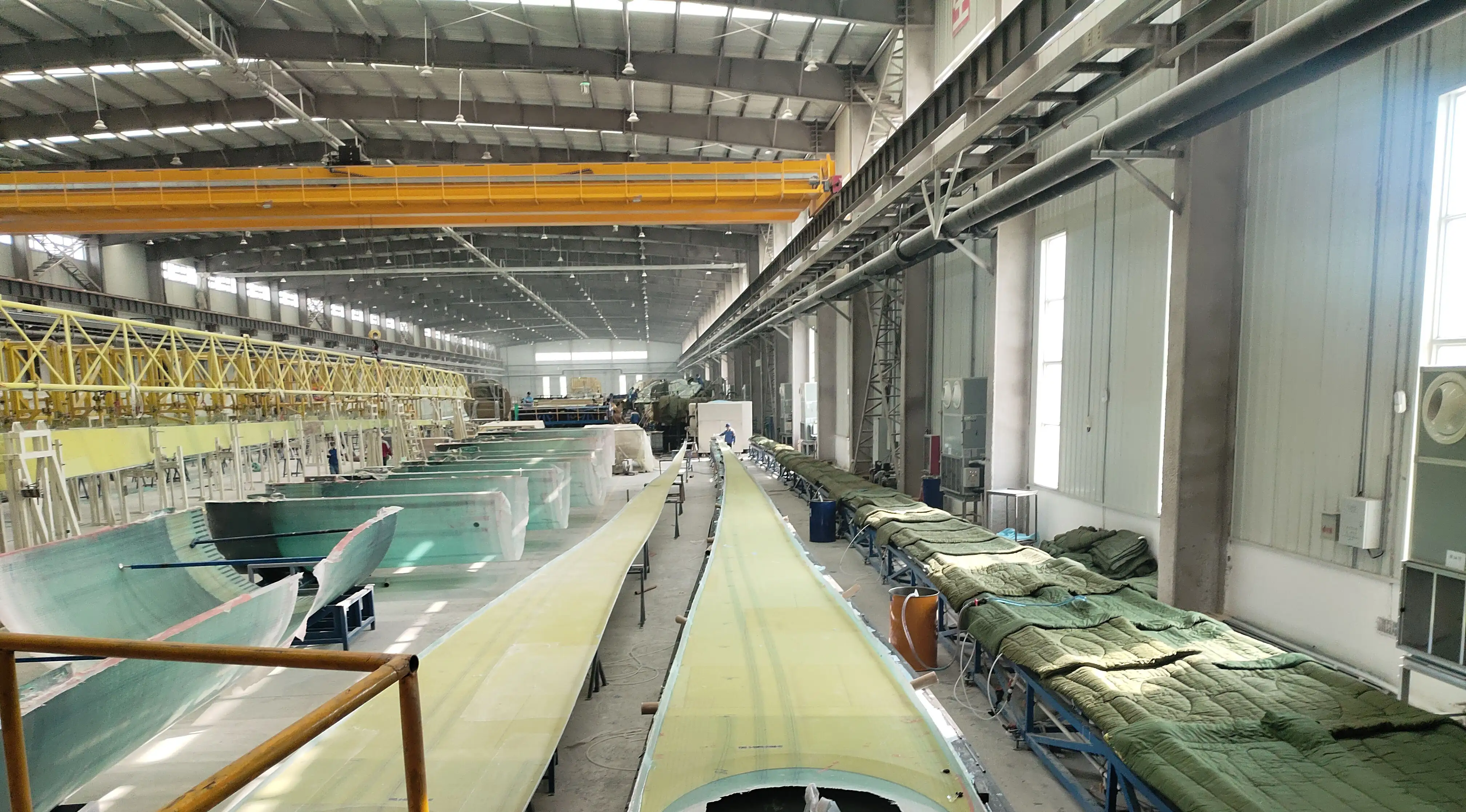
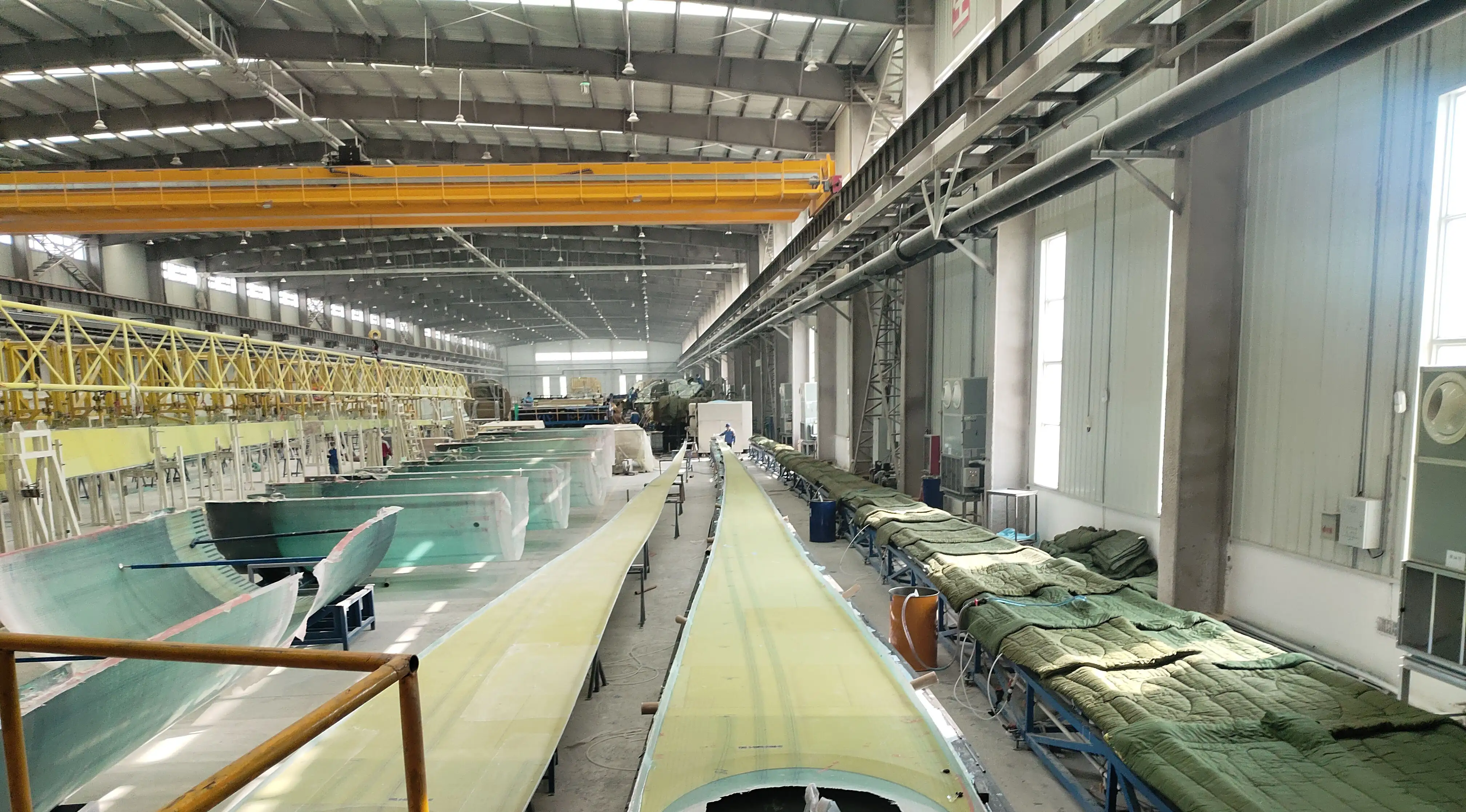
Vacuum leaks produce ultrasonic waves, which are captured by the microphone array of the CRYSOUND acoustic imaging device. By processing these signals in real time, the device can quickly and accurately pinpoint the exact location of leaks. This technology allows anyone to perform comprehensive, reliable, and actionable leak detection with ease.
Vacuum leaks produce ultrasonic waves, which are captured by the microphone array of the CRYSOUND acoustic imaging device. By processing these signals in real time, the device can quickly and accurately pinpoint the exact location of leaks. This technology allows anyone to perform comprehensive, reliable, and actionable leak detection with ease.
Vacuum leaks produce ultrasonic waves, which are captured by the microphone array of the CRYSOUND acoustic imaging device. By processing these signals in real time, the device can quickly and accurately pinpoint the exact location of leaks. This technology allows anyone to perform comprehensive, reliable, and actionable leak detection with ease.
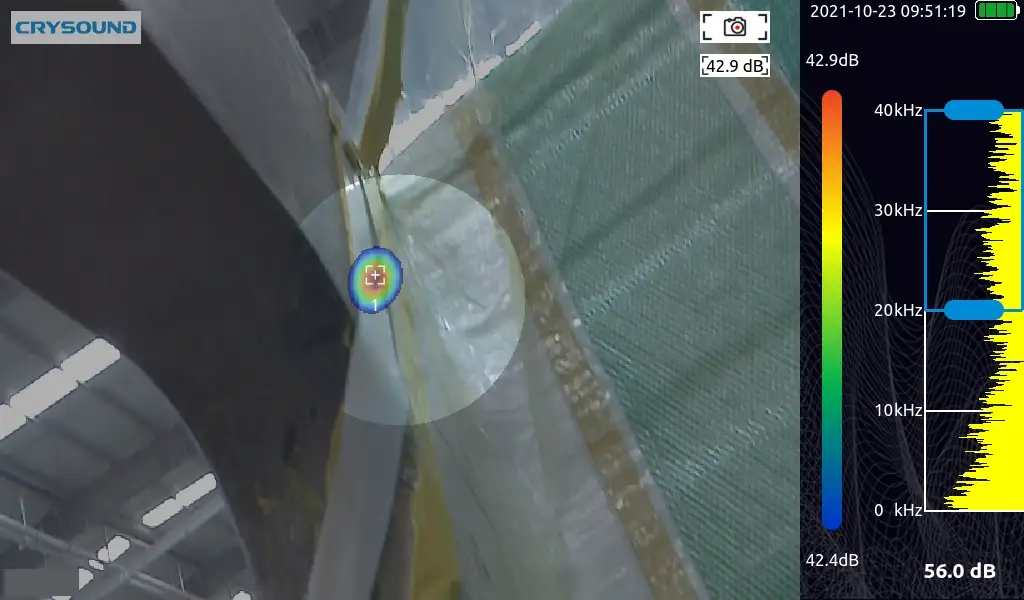
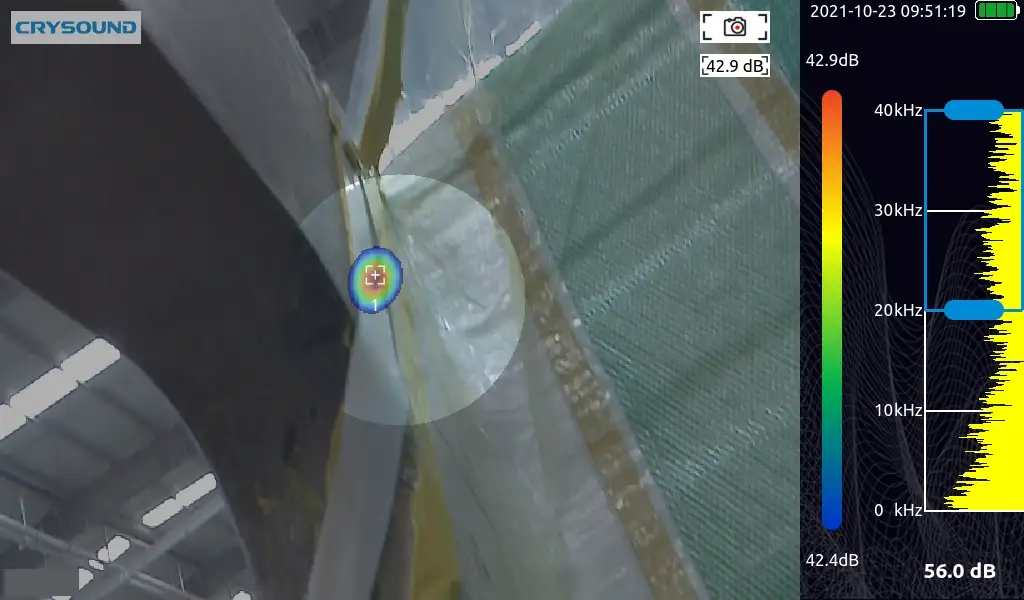
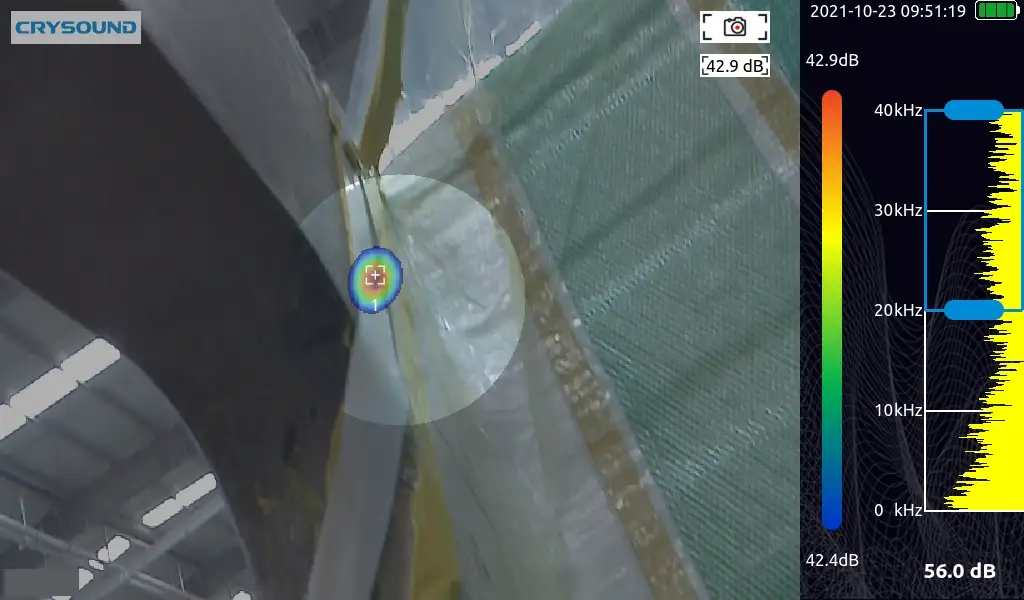
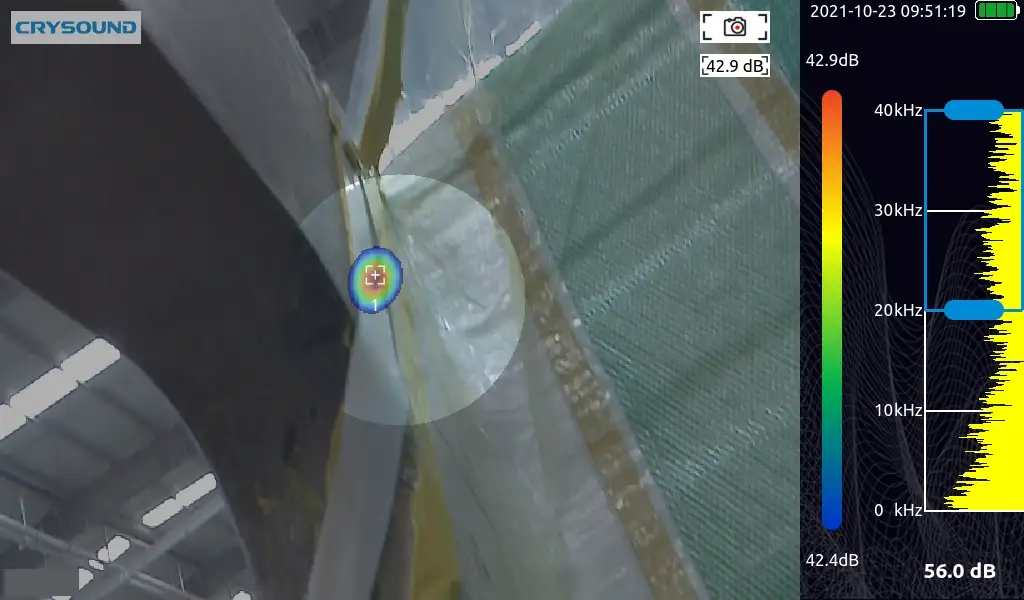
No-contact scanning and testing of mating sealing surfaces from a distance enable non-destructive air-tightness testing of vehicles and vessels.
No-contact scanning and testing of mating sealing surfaces from a distance enable non-destructive air-tightness testing of vehicles and vessels.
No-contact scanning and testing of mating sealing surfaces from a distance enable non-destructive air-tightness testing of vehicles and vessels.
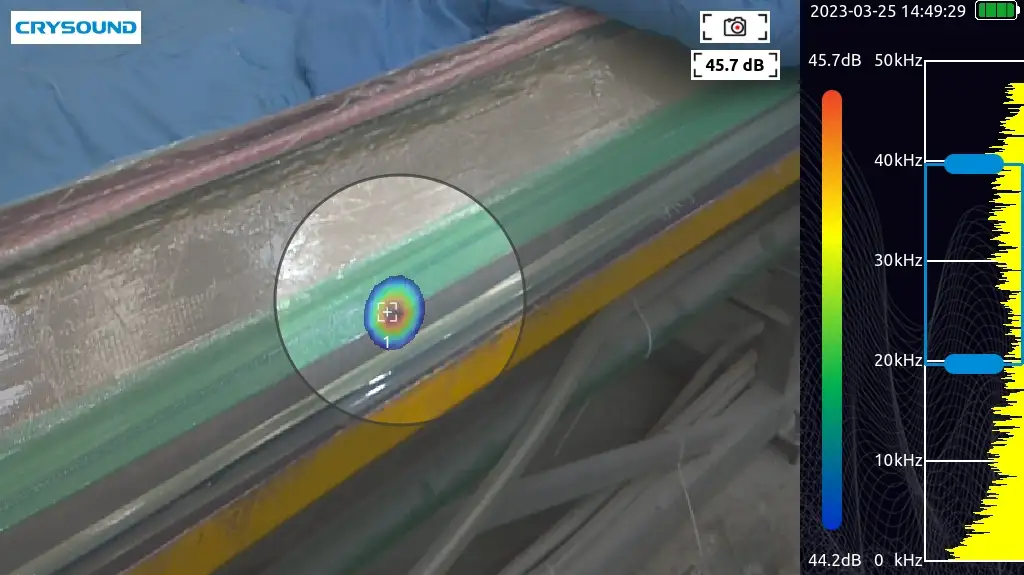
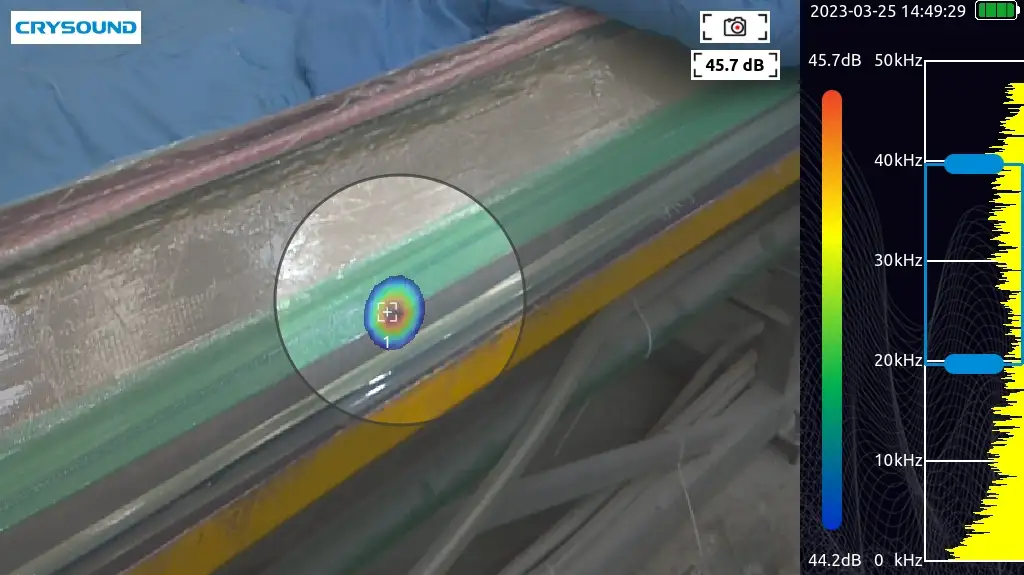
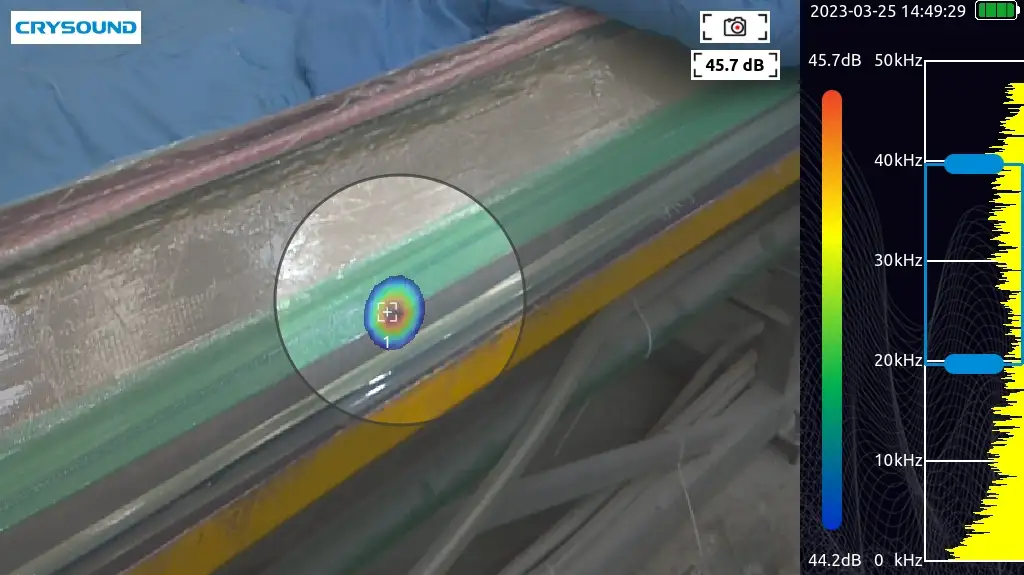
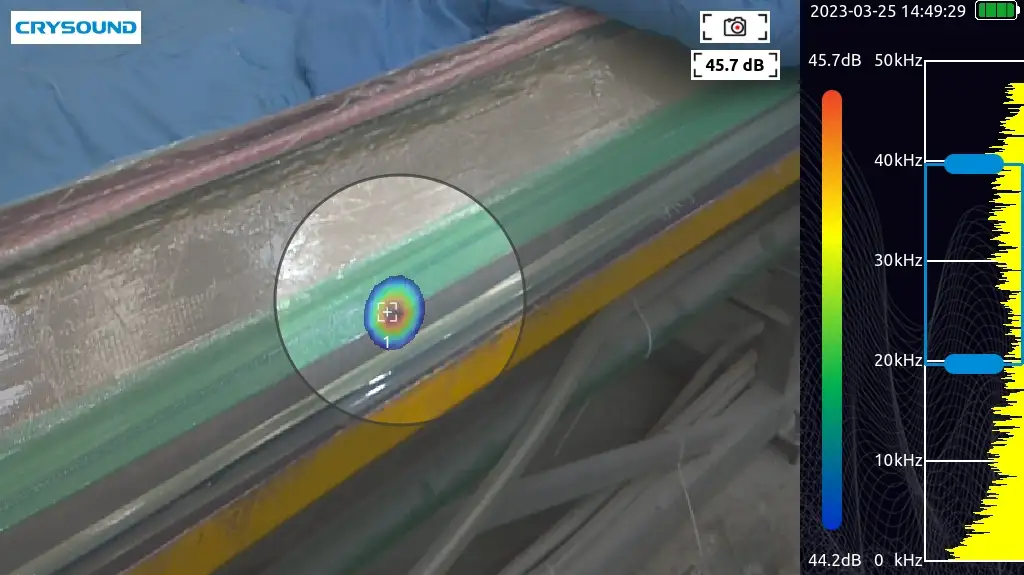
Acoustic imaging is a novel technology that provides a real-time visualization of leaks from a distance. With an acoustic imaging camera, anyone can pinpoint vacuum leaks 10x faster than traditional methods.
Acoustic imaging is a novel technology that provides a real-time visualization of leaks from a distance. With an acoustic imaging camera, anyone can pinpoint vacuum leaks 10x faster than traditional methods.
Acoustic imaging is a novel technology that provides a real-time visualization of leaks from a distance. With an acoustic imaging camera, anyone can pinpoint vacuum leaks 10x faster than traditional methods.




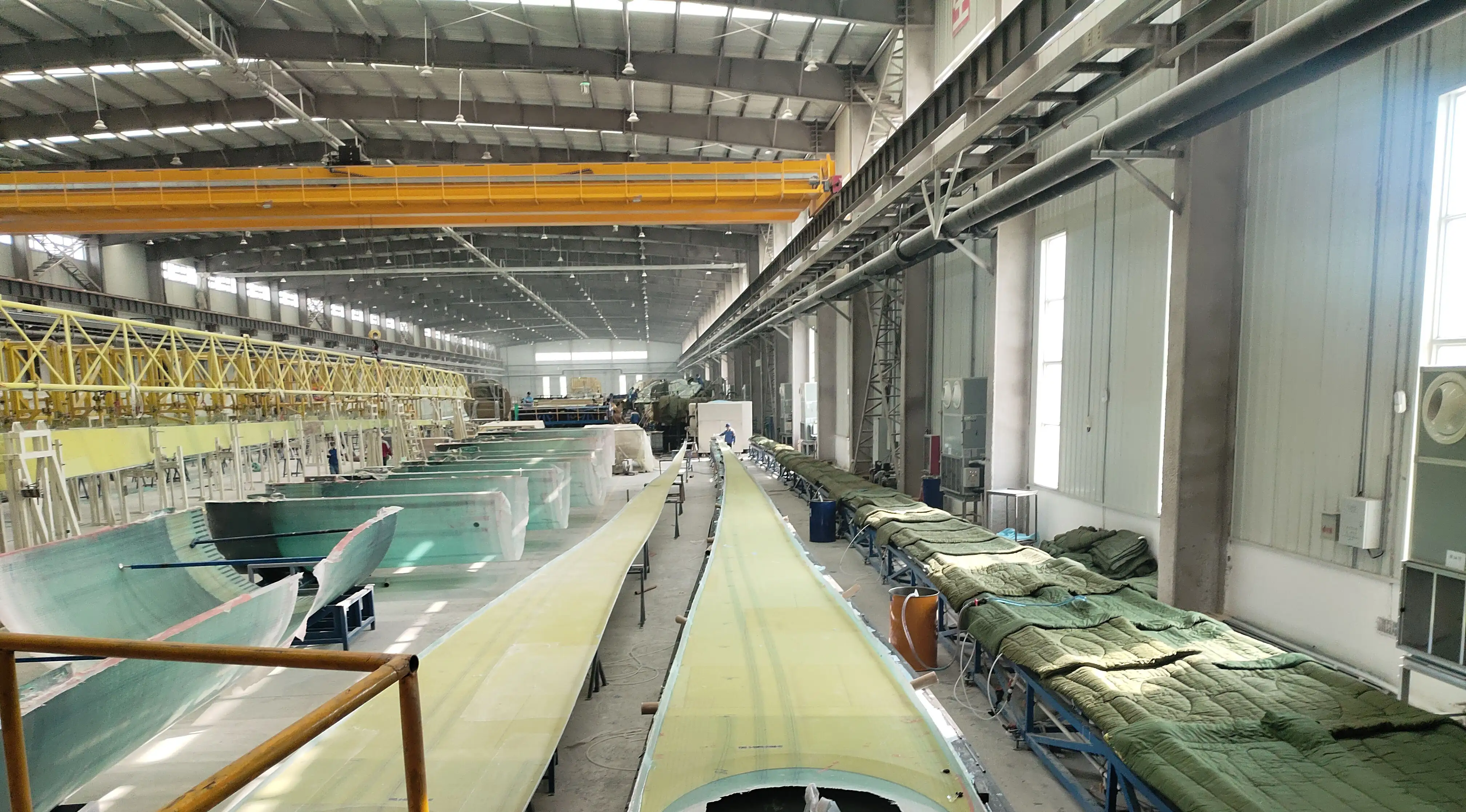
Composite materials are widely utilized in the wind energy sector. Gas permeability testing of these materials is primarily conducted to assess their ability to prevent the penetration of gases or liquids, ensuring optimal product performance in various environmental conditions.
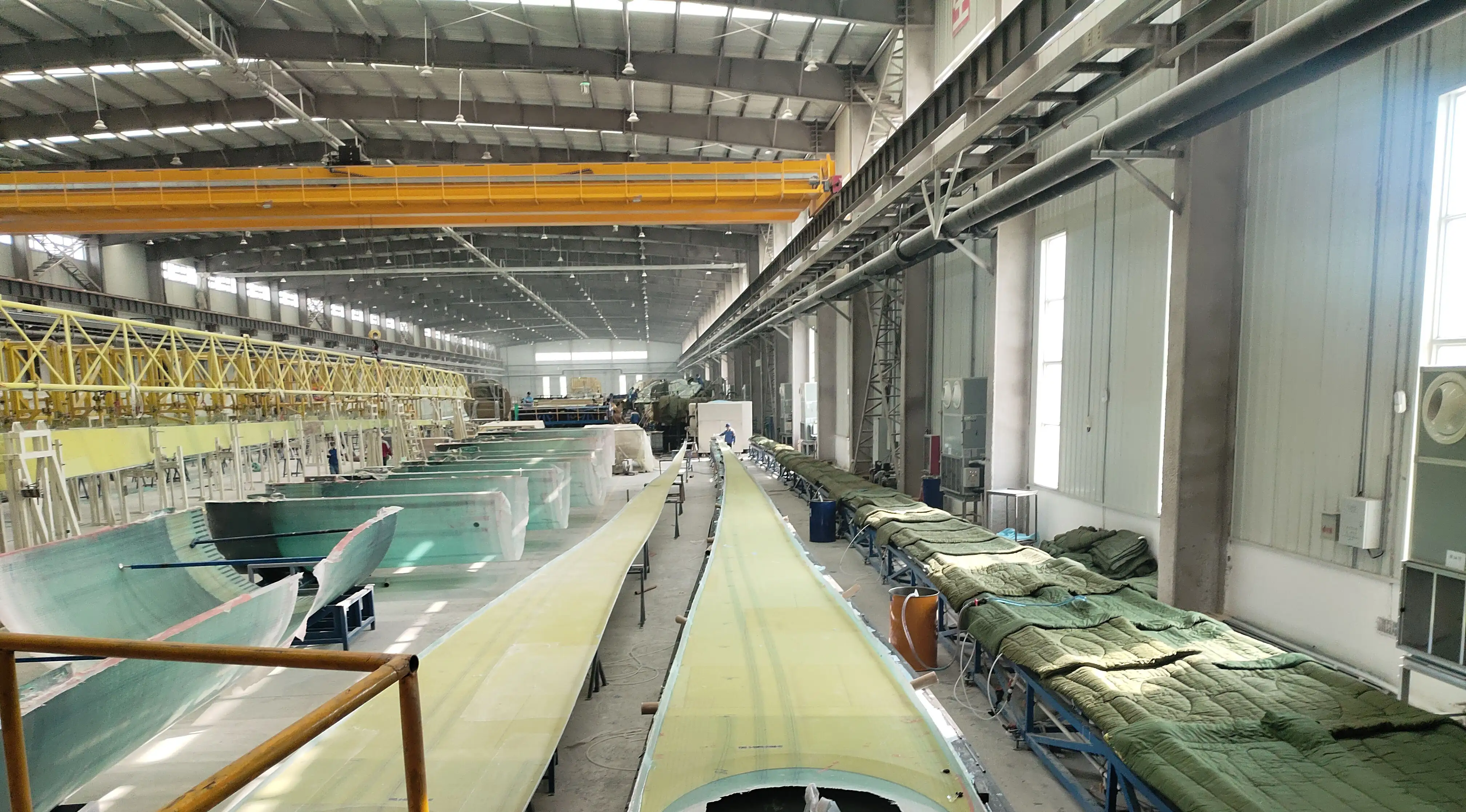
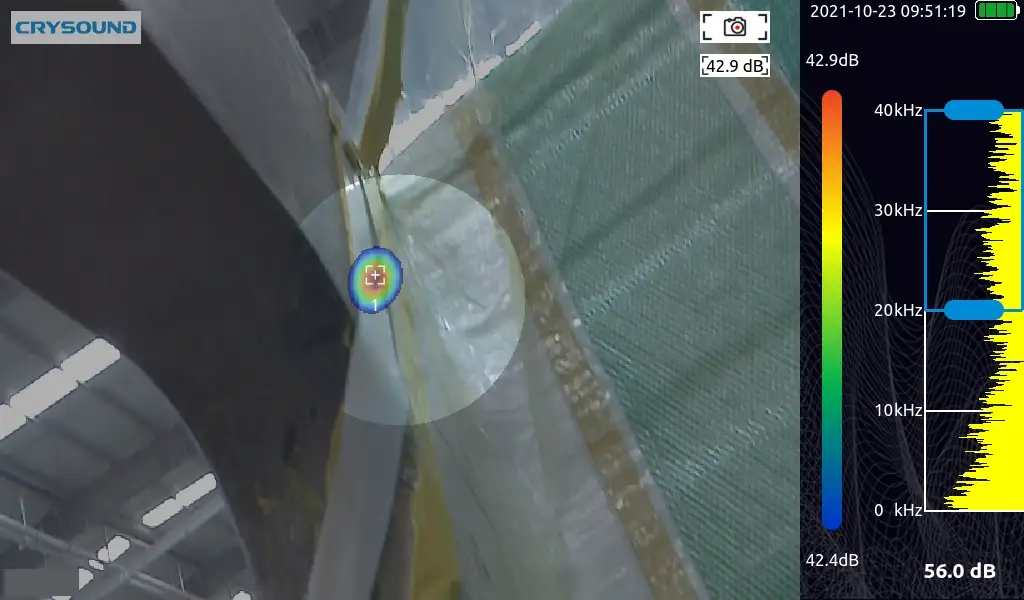
Vacuum leaks produce ultrasonic waves, which are captured by the microphone array of the CRYSOUND acoustic imaging device. By processing these signals in real time, the device can quickly and accurately pinpoint the exact location of leaks. This technology allows anyone to perform comprehensive, reliable, and actionable leak detection with ease.
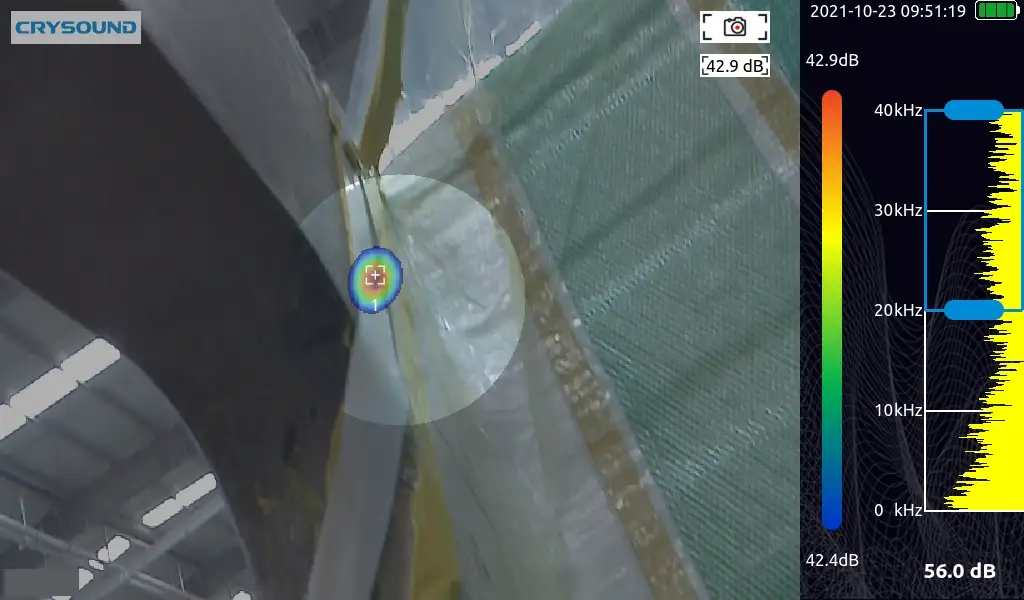
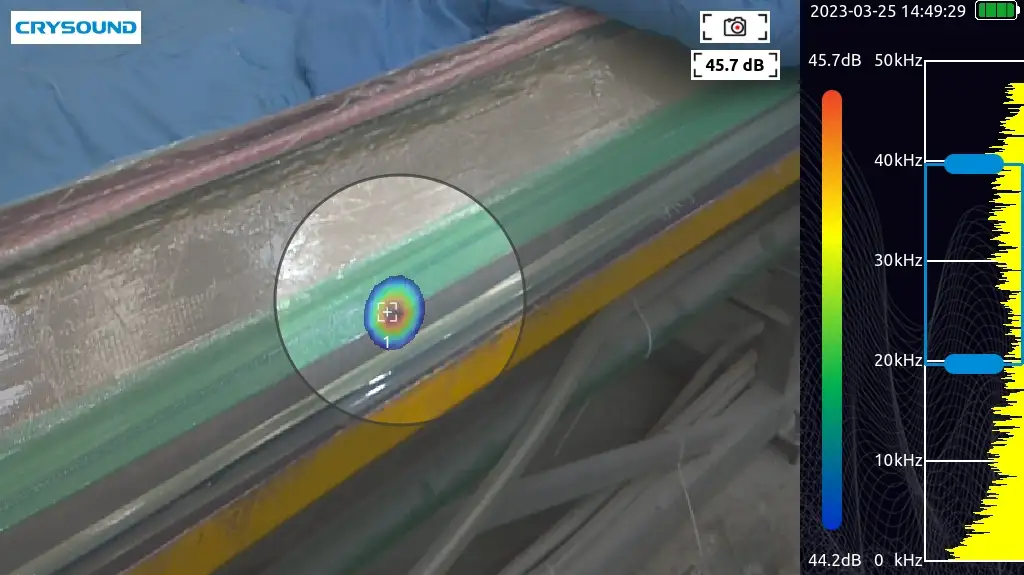
No-contact scanning and testing of mating sealing surfaces from a distance enable non-destructive air-tightness testing of vehicles and vessels.
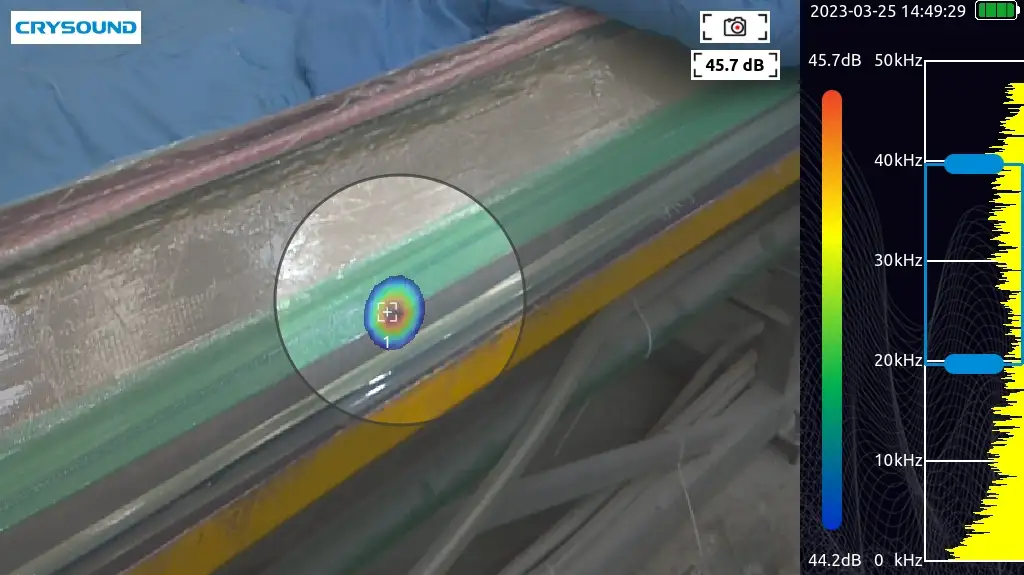

Acoustic imaging is a novel technology that provides a real-time visualization of leaks from a distance. With an acoustic imaging camera, anyone can pinpoint vacuum leaks 10x faster than traditional methods.

System Devices
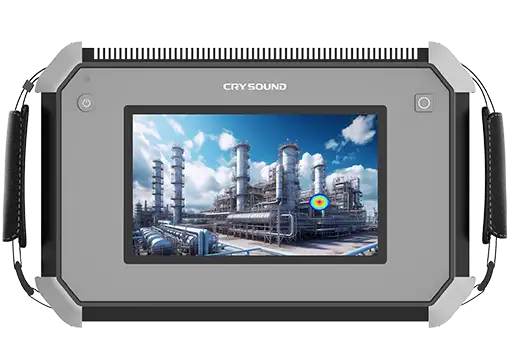
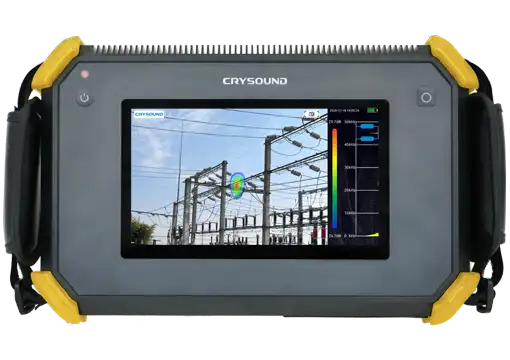
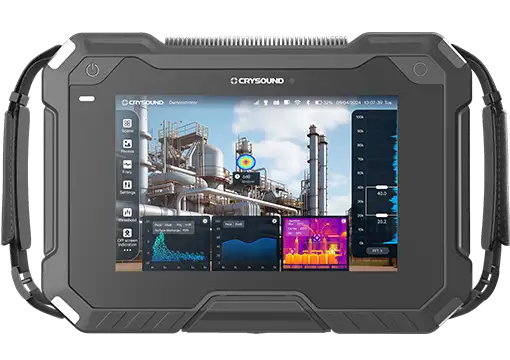
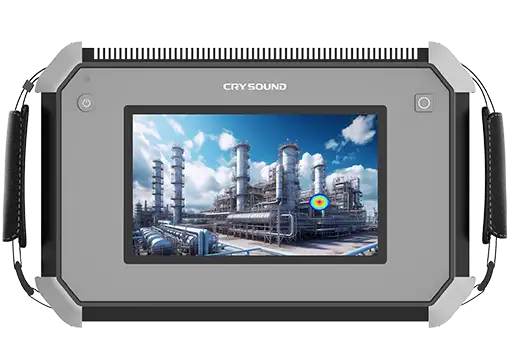
The CRY2620 Industrial Acoustic Imaging Camera is designed for ease of use and quick operation. Its robust aluminum alloy shell ensures durability, making it adaptable to complex and changing work environments. The device provides a real-time sound image display, significantly accelerating the detection of pressurized or vacuum leaks compared to traditional methods.
The CRY2620 simplifies testing with just two adjustable parameters: test frequency range and dynamic range, covering most testing needs.
It offers multiple modes, including camera and video modes, along with flexible on-site data recording. The large-capacity TF storage card is expandable, allowing for quick export and reporting of test results.
This device helps enterprises minimize losses from gas leaks and other accidents, enhancing overall operational safety.
?
.png)

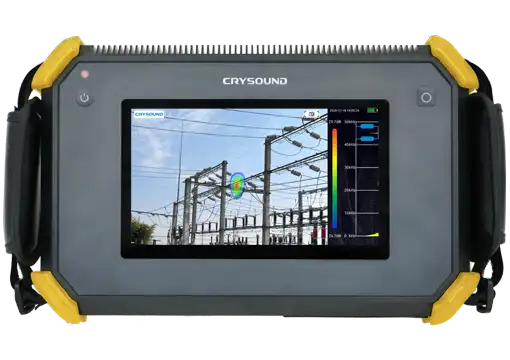
The CRY2623 is a 128-mic industrial acoustic imaging camera that is user-friendly and requires minimal training. Its durable aluminum alloy shell is built to withstand complex and variable working conditions. The device offers real-time acoustic imaging, significantly accelerating the detection of pressurized or vacuum leaks compared to traditional methods. It supports both photo and video modes for flexible on-site data recording. With an expandable large-capacity TF storage card, test results can be quickly exported and reported. The CRY2623 helps enterprises reduce safety risks and minimize economic losses associated with gas leaks, partial discharges, and other malfunctions.
.png)

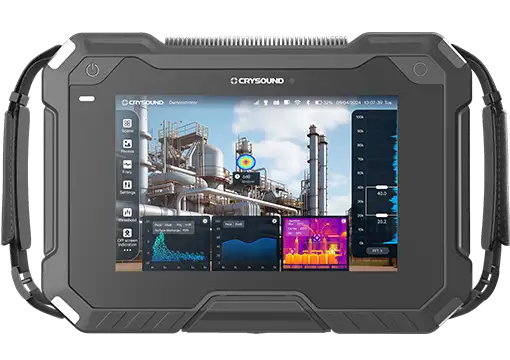
Introducing CRYSOUND’s cutting-edge acoustic imaging camera, revolutionizing industrial inspections with advanced capabilities. The CRY8124 acoustic imaging camera excels at pinpointing leaks, identifying electrical partial discharge, and detecting mechanical deterioration. Setting a new standard for sensitivity and efficiency, the CRY8124 boasts 200 microphones (the most in the industry). The device detects smaller leaks and partial discharges from greater distance than any other handheld acoustic imaging camera on the market.
The CRY8124 reporting software allows offline analysis, editing, and report generation, simplifying regular maintenance routines.
Elevate the effectiveness of your industrial inspections with CRYSOUND’s acoustic cameras.
.png)
